extension and retraction time
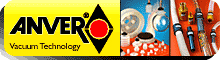
Home | Pneumatics Online › Forums › extension and retraction time
- This topic has 3 replies, 1 voice, and was last updated 4 years, 7 months ago by
admin.
- AuthorPosts
- June 2, 2007 at 9:17 am #19572
admin
ParticipantI have an application where I use a double acting linear drive that, through a mechanical linkage, makes another piece swing. The swinging is controled by a machne cycle count (same count for extended position as for retracted position.)
The problem is, the actuator takes longer to retract than it does to extend (less than one second, but that is enough time for the machine to dump one extra piece in the container it is filling.)
I have already checked the lubrication of the mechanical assembly, and it's working properly (sure enough it's not friction free, but I think it would be negligible, as the piston is moving _only_ a thin metal plate of 2" by 5".) Line pressure is also within range, and piston is also working OK (it must be a design/selection problem, because I have it in all 5 machines of the line).What is causing the difference in extension / retraction time?
With the same actuators I have now, what can I change to make the swing last the same time for each side??
Would it be a better idea to have a rotary actuator? (I wouldn't like to incur in extra expense if it's not going to work…)
Thanks for your guidance!!
G.November 25, 2020 at 9:47 am #20924admin
ParticipantRegulate the pressure to the Cap (Blind) end of the cylinder to some lower figure than the pressure to the Rod end. Your problem is unequal areas that gives unequal force for extend and retract, therefore uequal time cycles. A Double Rod Cylinder would also work but would be an expensive change.
November 25, 2020 at 9:47 am #20925admin
ParticipantWithout seeing the design, gravity may be assisting your motion in one direction and resisting motion in the other direction. Your load may also be more than this plate if it is pushing product in one direction but not the other. If your actuator is a single rod end then the different area’s (or volumes) in each direction could also cause different stroke times. A pressure regulator or flow control (typically choking the exhaust side) could be used to ‘slow’ down the offending motion.
November 25, 2020 at 9:47 am #20926admin
ParticipantCurt wrote:\; Without seeing the design, gravity may be assisting your motion in one direction and resisting motion in the other direction. Your load may also be more than this plate if it is pushing product in one direction but not the other. Regardless of what the reason for the different forces, different pressures will make the actuator move quickly and smoothly. The only problem with air cylinder action comes when the load is changing while it is in motion. Go to oil in those cases.
- AuthorPosts
- You must be logged in to reply to this topic.